Open-source Framework for 3D Ultrasound Modeling in Fiber-reinforced Composite Parts
Fiber-reinforced polymers are commonly implemented in the aerospace industry. Like any other part, they must be routinely inspected for defect. A method that has had rapid adoption is ultrasound inspection. Ultrasound modeling of composite parts means accounting for anisotropy and geometric complexities. Simulator-based techniques are often implemented to accomplish this task, but many are subscription based. The research involves the adaptation of an open-source solver for seismic wave modeling to an ultrasound wave modeling in composites setting.
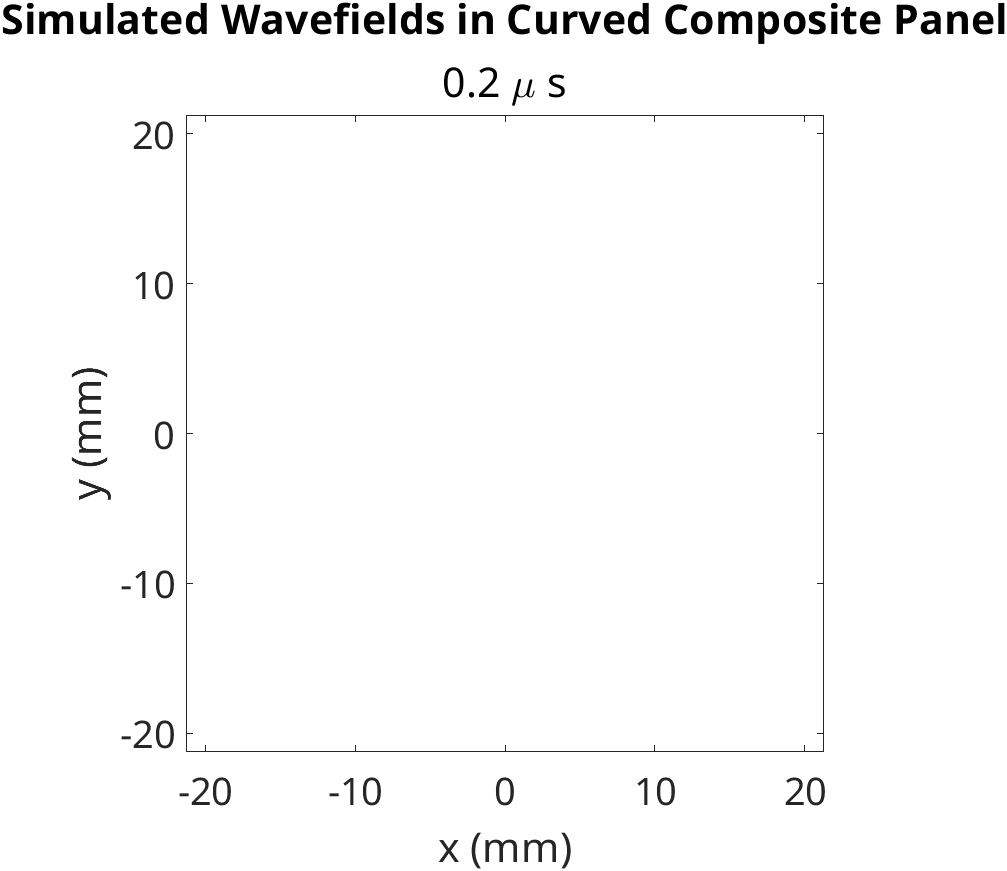
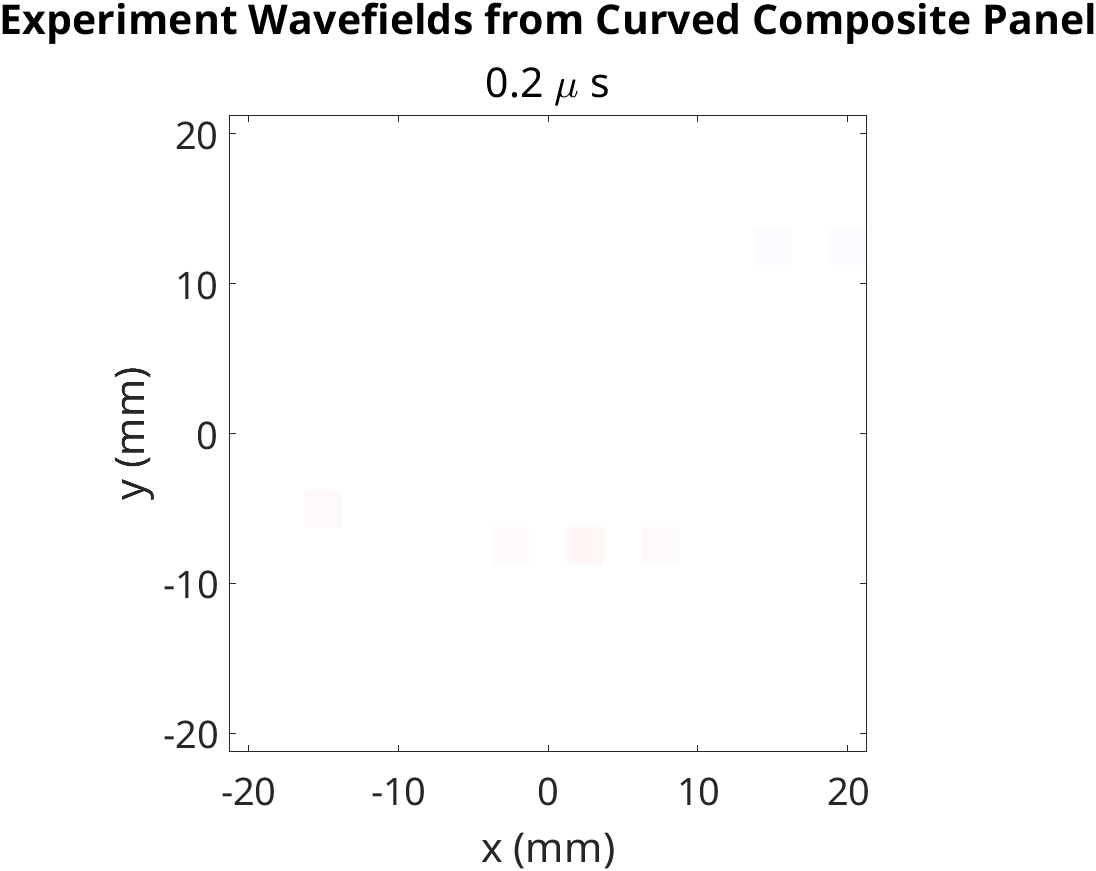
The goal of this research sector is to develop an open-source package for accurately calculating ultrasound wavefields within composite parts, mostly within a lamb-wave setting. The benefits of obtaining the fully spatially characterized ultrasonic wavefield is defect detection and monitoring of the primary material characteristics. However, to accomplish this, an accurate wave simulator is needed. Fiber-reinforced composite parts complicate this because of their inherent anisotropy as well as potentially complex geometrical parameters, such as shells. This necessitates a robust wave simulator which accounts for these properties. This research explores SPECFEM3D as a potential open-source framework for this wave modeling problem. To benchmark it, the lab has outsourced the creation of several carbon-fiber reinforced laminates, which are created within the university of Alabama. This project has already had initial success in wave modeling in specific locations on the composite panel, and is aiming to provide an accurate full wavefield simulation and verify with lab data.
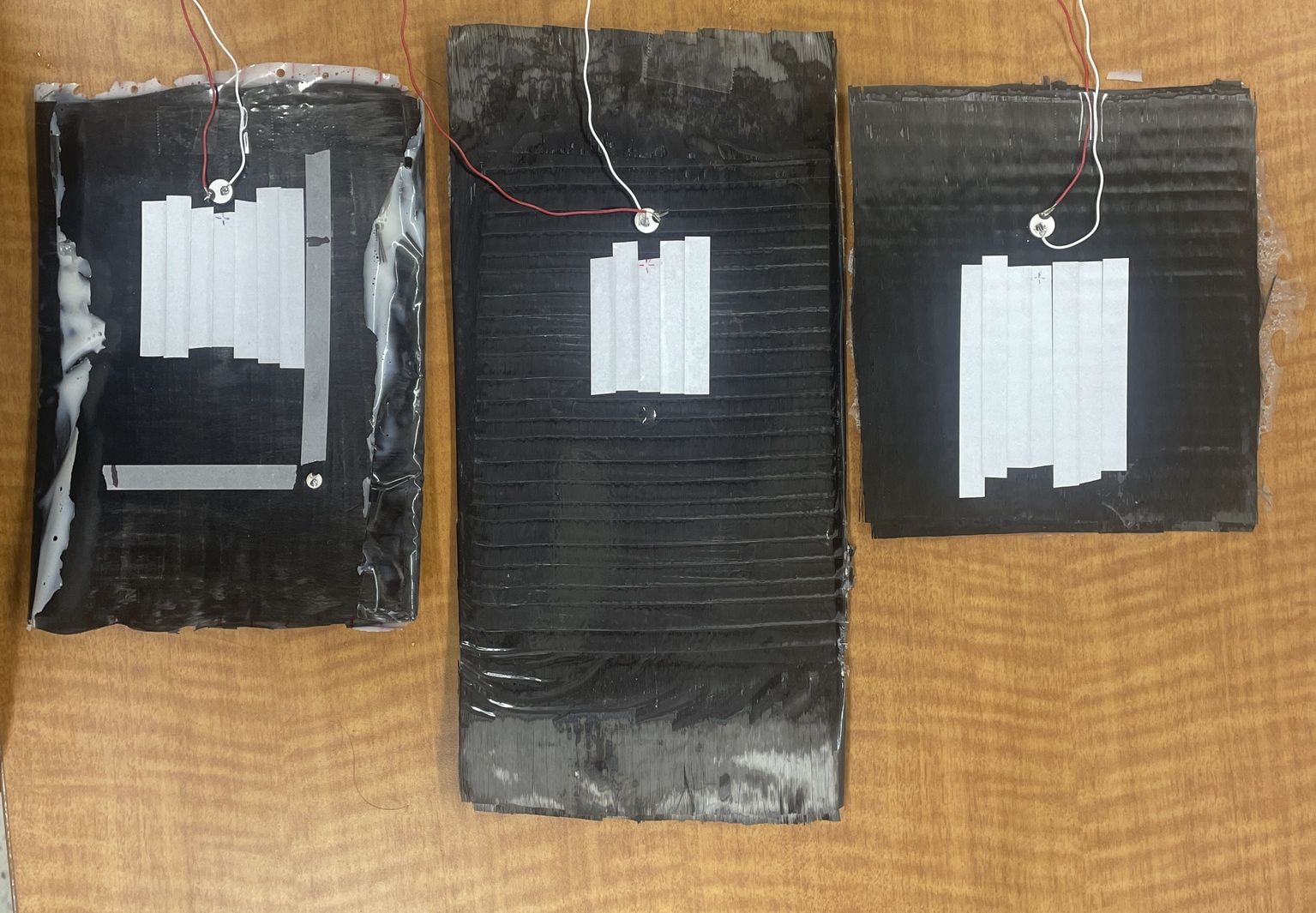
Publications: (Refer to the publication page for detailed paper links)
- Coming soon...